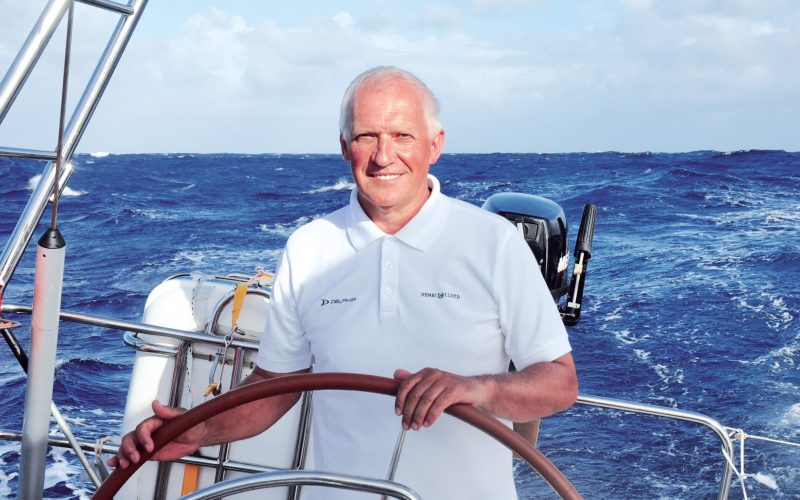
Firma nieustannie śledzi konkurencję, by ich marka była prekursorem nie tylko na wodzie, ale również na drodze do innowacji. Z Wojciechem Kotem spotykamy się niespełna rok po uroczystym otwarciu Centrum Badawczo-Rozwojowego Delphia Yachts. Inwestycja wyniosła 12,7 mln zł i została wsparta unijnym dofinansowaniem w wysokości 4,1 mln zł. Nowo otwarty zakład zajął się opracowywaniem nowoczesnych materiałów do produkcji jachtów nowej generacji i obecnie rozwija tę dziedzinę, aby niebawem pochwalić się pierwszymi rezultatami. Jak doszło do inwestycji? Wypracowaliśmy ideę, do której popchnęły nas osiągnięcia konkurencji z Europy Zachodniej oraz zmiany ekonomiczne polskich realiów. Żeby utrzymać się na wysokiej pozycji, musieliśmy działać. I działają. Nanotechnologia w przemyśle stoczniowym dynamicznie rozwija się w niewielkim Olecku na Mazurach, gdzie mieści się serce firmy – stocznia, w której odbywa się produkcja, oraz nowo powstałe centrum.
O jakich nanomateriałach możemy mówić w przypadku produkcji jachtów?
Wojciech Kot: Trwają badania nad kilkoma rodzajami nanomateriałów, natomiast na ten moment możemy powiedzieć przede wszystkim o technologii otrzymywania nanomateriałów węglowych – grafenu płatkowego i nanorurek węglowych. Przystępując do badań, na początku określamy zestaw cech, które musi spełnić dany materiał. W naszym przypadku najczęściej jest to twardość, kruchość czy odporność na ścieranie. Jachty wysokiej jakości to nasz znak rozpoznawczy, który wypływa z naszej stoczni w Olecku na szerokie wody.
Nowe materiały dają nowe możliwości?
Zdecydowanie tak. Często porównuję proces konstrukcji do butów biegacza. Jeśli producent w ramach prac technologicznych otrzyma nową, lepszą podeszwę, to automatycznie będzie chciał pracować nad jakością pozostałej części obuwia. Będzie skupiał się na pracy nad całością produktu. Podobnie jest z jachtami. Stosując nową technologię, nie skupiamy się jedynie na jednym elemencie. Staramy się wykorzystać rozwiązania dla całego statku. Aby w pełni dostosować się do nowych osiągnięć technicznych, pracujemy z projektantami również nad designem jachtu. Przykładowo: wprowadzając nanomateriały do produkcji jachtów, skupiliśmy się również na parametrach nautycznych – poprzez nanomateriały nasi technolodzy dążą do zmniejszenia oporów wodnych, aby jachty były jeszcze szybsze. W konsekwencji musimy wziąć pod uwagę, że uderzenia w fale również będą się odbywały z większą mocą. W ten sposób dochodzimy do konieczności zadbania o burtę, która będzie w stanie minimalizować uderzenia. Produkcja w oparciu o ulepszone technologie to system naczyń powiązanych, gdzie każdy element musi zostać oceniony na nowo.
Duży może więcej?
To chyba najlepsze podsumowanie naszych starań o powołanie do życia centrum badawczego, którego osią było zaangażowanie świata nauki. Połączenie sił i podjęcie współpracy z Instytutem Chemii Przemysłowej w Warszawie, Politechniką Gdańską i Politechniką Warszawską zapewniło cenne wsparcie naukowe, którego nam brakowało. Możemy tu mówić o udanym przykładzie transferu wiedzy ze środowiska naukowego do biznesu. Wzorem Doliny Krzemowej, która skupia grono specjalistów, postanowiliśmy stworzyć odpowiednie warunki pracy dla tutejszych inżynierów, naukowców, którzy wspólnie są w stanie zdziałać więcej. Nie zawiedliśmy się.
To nie jest Państwa pierwsze spotkanie z nowymi technologiami?
Rzeczywiście od lat staramy się być obecni na ścieżce innowacji. Nie wszystkie nasze projekty były udane, jak w każdej branży zdarzały się porażki. Możemy się natomiast pochwalić dbałością o środowisko naturalne i bezpieczeństwo pracowników. Z tych wartości wywodzą się takie inicjatywy, jak technologia infuzji, która minimalizuje poziom emisji styrenu i pozwala uzyskać laminat najwyższej jakości. Nie bez echa przeszła również pięcioosiowa maszyna CNC, która pozwoliła na precyzyjny druk poszczególnych elementów jachtu z zastosowaniem techniki 3D. Każdego roku zabezpieczamy finanse na rozwijanie projektów proekologicznych. Zaczęliśmy od podstaw, takich jak utworzenie specjalnego stanowiska przeznaczonego do sortowania odpadów, aby przejść do większych projektów typu wprowadzenie kotłowni olejowej zamiast węglowej. A to na pewno nie koniec inwestycji tego rodzaju.
Proces produkcji w Delphia Yachts
W projektowaniu jachtów pośrednio uczestniczą ich nabywcy. To oni dzielą się z firmą bezcennymi uwagami, czego w danym modelu brakuje, co jest zbędne, a co mogłoby być lepiej wykorzystane. Można tu śmiało mówić o firmie z tradycjami, która nie tworzy wyłącznie po to, by zarabiać, ale również po to, by dawać ludziom wartość i dzielić się pasją do żeglarstwa. Relacja z rynkiem i unikalny, funkcjonalny design to jedne z cech, które stworzyły tę rozpoznawalną na całym świecie markę. Logo Delphia Yachts można ujrzeć w marinach na całym świecie.
Centrum B+R to konieczność dzisiejszych czasów
Wojciech Kot, współzałożyciel Delphia Yachts, nie wyobraża sobie, aby jego firma nie miała działu B+R (Badania i Rozwój) i nie pracowała nad technologią, która w przyszłości będzie mogła zastąpić te rozwiązania, które są wykorzystywane obecnie. Coraz większy nacisk kładzie się na materiały, które zapewniają jachtom nie tylko lepsze parametry techniczne, ale i bezpieczeństwo. Aby polska stocznia mogła zaskoczyć świat unikalnym rozwiązaniem, potrzebne były pieniądze i specjalistyczna wiedza naukowa. Jest rok 2018, firma ma jedno i drugie. Branża z niecierpliwością czeka na wyniki zespołu badawczego.